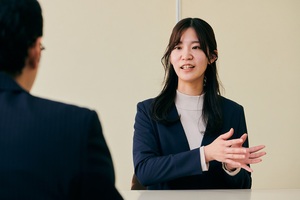
■包装材開発の課題
──今、メインになっている最終製品は何ですか。
住田 スマートフォンと電気自動車が多いです。ほかにもパソコンやドローンにも使われています。
──電気自動車を開発していく上で、理想の電池とはどういうものですか。
住田 車は2、3年使えればいいものではなく、使われている間は絶対に故障があってはいけないものです。長く乗られることも想定して10年以上安全に使えることが求められます。
──その実現に向けて、DNPとしての課題は何でしょうか。
住田 大前提として、電池の内部に水などが入るのを防がないといけません。また、完璧に密閉できたとしても電池の中には化学反応を起こすようなものが入っているので、それにより通常範囲ではない高温領域に突然なってしまうこともあります。万が一の異常時も想定し、リチウムイオン電池をできる限り安全に使いこなせるように外装材や部材の開発が求められます。
──厳重に密閉すればいい、というものではないのですか。
住田 そうですね。充放電を繰り返す中で電池は少し中身が膨らんだり、縮んだりするので、それによって外装材も影響を受ける可能性があります。また、スマートフォンであれば人が落とすこともありますから、衝撃に耐える性能も必要です。車に搭載する電池も、舗装されてない道路だと衝撃や振動が加わったり、すごく寒暖差があったりするところで使われるかもしれません。バッテリーが入っているモータールーム(エンジンルーム)に影響を与えるかもしれない環境の変化を想定して、常にバッテリーを安全に保つことが求められています。
また、より電池の総数を減らしたり、電池を正常に動かすための部材に割くスペースを減らすことを目指して、高容量、高出力な電池が開発されています。例えば、今まで20個の電池を載せないといけなかったのが、10個で済むとその分スペースが空くので、車をよりコンパクトにすることもできます。電池の重量が減れば、輸送時のエネルギーや、搭載した車が走行するために使うエネルギーを減らせるため、環境配慮につながります。
──技術的に乗り越えるべき壁は、どういうところにあるんですか。
住田 実は、次世代電池は、中身に使う材料や、どこまでの温度で使うかなどがまだ決まっていない、手探りの状態で、さまざまな可能性を想定して外装材も進化させていかないといけません。社会や市場の変化に合わせて、お客様の課題やニーズは変わります。「〇〇の環境で使用することを想定し△△や●●の性能を高めたバッテリーを作ってください」という相談を受けたとしても、半年後には違うニーズが生まれ、別の性能を求められる、といったように開発にスピード感が必要だと感じます。「これ」という課題が1つに決まっていない状態で、時代を先読みしながら、社会や市場、お客様の変化についていかなければいけません。
──今の技術から、かなり飛躍する必要がありそうですか。
住田 今、私たちが作ってきたバッテリーパウチは事故がなく、高い信頼性を得られています。それでも今後もしかしたら電池の中身が変わっても外装材自体は今のまま使えるかもしれませんし、より高い性能が求められる可能性もあります。色々な可能性を想定し、中身などを変化させてみて、仕様を満たさなければ改良し、得意先のニーズと照らし合わせる、というサイクルを繰り返しています。